Uniting Design Excellence, On-Site Control & Proactive Checks for Lasting Timber Structures
With 22 years of timber engineering experience—and two decades spent on the front lines diagnosing and solving durability issues—I’ve encountered it all. Statistically, it’s rare for a building to face its full design earthquake, maximum snow load, peak wind gusts, or a severe wildfire. But water? We deal with it every day—in bathrooms, kitchens, mechanical rooms, and from driving rain. Pressurized pipes or a broken membrane can turn a minor drip into major failure in just a few years.
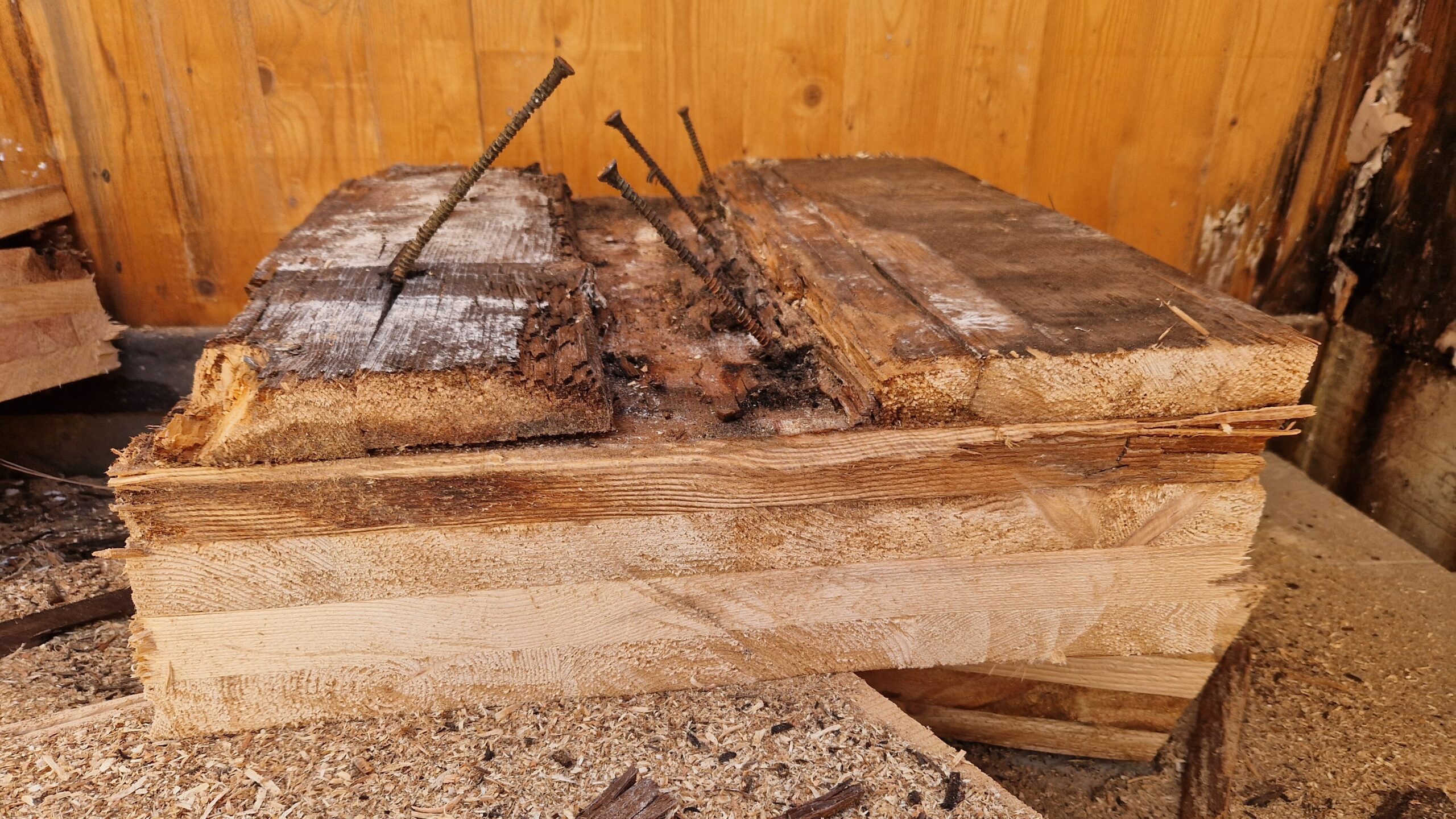
I know it’s not always comfortable to discuss timber’s vulnerabilities—after all, we at Ergodomus love wood for its beauty, performance, and sustainability. Yet the moment has come to shine a light on these challenges—for the future of timber construction and our planet’s health. In this article, we’ll share lesser-known insights from real projects, so every stakeholder can specify, build, and maintain truly durable timber structures.
And yes—durability failures often lead to insurance headaches, with rot and water-damage exclusions driving up claim costs.
Design Excellence
Durability must start at the drawing board. From Day 1, architects, structural & MEP engineers, envelope specialists, and landscape designers need to:
- Eliminate water-stagnation zones with correct slopes and generous overhangs
- Specify accessible flashings and water-shedding details
- Conduct performance testing of critical details under real conditions
- Account for material ageing (e.g., UV exposure) during installation and throughout the building’s life—always with a Plan B for long-term resilience
Durability cannot be “subcontracted” to the builder—it’s as fundamental as structural, MEP, and architectural design.
On-Site Quality Assurance
Even flawless drawings fail without precise installation and strict quality control. Designers and site managers share heavy responsibility to:
- Verify membrane continuity before enclosure
- Inspect flashings, joints, and connections at every phase
- Train trades on durability-critical procedures
Remember: materials don’t fail—humans do. A poorly sealed washing-machine penetration today can be tomorrow’s rot.
Guess what the third, unpredictable factor is?
Occupant Behavior: The Wild Card
No matter how well you design or build, you cannot control how occupants use the space:
- Public buildings (e.g. schools, libraries) may sit empty for weeks—making leaks invisible to anyone on site.
- In homes and offices, unnoticed leaks from plumbing fixtures or tenant modifications can silently invite decay.
It’s our duty to educate users and facility teams—but ultimately, habits are unpredictable.
Murphy’s Law: The “Unlucky” Factor
Murphy’s Law applies to timber durability every step of the way: during installation—“Anything that can be installed incorrectly, will be”—and over the building’s life—“If there’s a worse time for something to go wrong, it will happen then.” Random failures—membrane punctures, hidden leaks, freak storms, earthquakes, heavy snow—are as unpredictable as wind or live loads. Structural engineers address unknowns with safety factors and load combinations; durability design must do the same. You can’t rely on a single membrane. Instead:
- Build redundancy into materials and details
- Plan regular inspection protocols
- Keep a robust Plan B ready for rapid response
What to Do When Problems Arise
At the first sign of moisture or rot, perform a root-cause analysis: what failed, where, and why? Remedies vary by element (roof, slab, wall, beam, column, connection) and damage extent:
- Minor leaks: resealing or local membrane patch
- Moderate breaches: targeted membrane replacement and detail upgrade
- Severe decay: remove and replace rotten timber with new certified sections
Experienced structural engineers must oversee every step, carrying out global and local structural analyses before and after repairs. The sooner problems are identified, the better—and the easier—the repair will be.
For privacy reasons, project photos have been re-elaborated.
Monitoring: An Investment, Not an Expense
A moisture-alarm system that alerts when timber exceeds ~20 % moisture content is “condicio sine qua non“ (a condition without which it cannot be) for durability. Would you drive a car without warning lights? A proper monitoring network:
- Detects hidden issues before they escalate
- Enables early intervention
- Preserves asset value over decades
It’s essential in spaces left unoccupied for long periods, like schools during summer break.
The 2 images below show the moisture changes in a real case, water leakage. Courtesy of WoodControl.
Why Timber Can Rot—Fast
Timber needs only water + oxygen. If both persist above 10–15 °C, rot microbes can halve a panel’s life in as little as two years. Think of Venice’s hourglass-shaped briccole: wave action cycles wood through wet and dry, accelerating decay. Early rot hides behind finishes—active monitoring is the only reliable detection method.
![]() |
“Briccole in Venice”: the hourglass shape is clear. Flickr (license CC BY-SA 2.0) 5244_49b342-8a> |
![]() |
The 3 elephants can’t be in the same room: Water, Oxygen, Timber. 5244_d9aa04-ab> |
Water-Permeation Poll
How long does water take to soak through a 200 mm CLT panel with a slight membrane breach and concrete screed? Answers range from hours to months—a true measure of your reaction time when leaks occur. We’ll reveal the results in a couple of weeks, so cast your vote in our LinkedIn poll and stay tuned!
![]() |
🔍 POLL: Water vs. CLT – How Fast Would You Notice the Leak? Imagine a 200 mm, 5-ply CLT slab with an impermeable membrane and 50 mm screed above. A tiny breach lets water drip at 15–20 drops/min onto the membrane. The CLT underside is fully exposed. How long before you’d spot moisture on that visible timber surface?
|
Proactive Health Check for Existing Buildings
If your timber building has been standing unmonitored for years, schedule a semi-invasive inspection of key elements—roof, slab, walls, beams, columns. A skilled technician, armed with your drawings and user feedback, will plan a bespoke diagnosis that uncovers hidden issues and lets you “sleep well” knowing any concerns are identified early and resolved.
Moisture sensors installed on a CLT panel.
Final Thoughts
Timber is a fantastic, sustainable material—and at Ergodomus, we champion it wholeheartedly. This article isn’t meant to scare you from using wood; it’s meant to raise awareness of real-world risks that can arise in years, not decades. Durability touches every discipline—architecture, structure, MEP, envelope, and construction—and continuous moisture management is vital for the building’s entire lifespan.
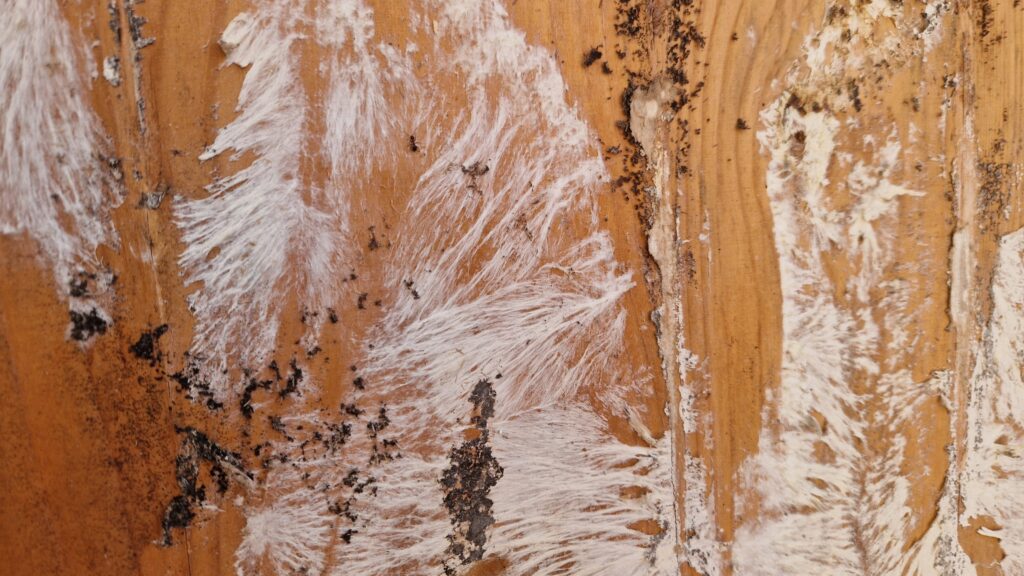
Let’s Hear Your Thoughts!
Join the LinkedIn discussion and share your insights:
- Have you faced durability issues in timber projects? What caused them?
- How do clients and designers around you perceive timber’s durability risks?
- Who should oversee long-term moisture monitoring in public buildings?
- Has monitoring saved you from major repairs—what was the payoff?
- How long do you think it takes for timber to dry by 1% moisture content (for example, from 18% to 17%)?
Ready lock in durability on your next timber project?
Don’t wait—contact Ergodomus today to build a future-proof structure, from design through daily use.
Drop a comment on LinkedIn here or share this article with a colleague who’s exploring timber buildings.