Parma, a charming Italian city renowned for its cuisine, now boasts a new 6-storey building made entirely of Mass Timber. Our scope of work for this CLT building in Parma included structural analysis, production drawings and assembly drawings. Commissioned by Boraschi Case in Legno srl and designed by architect Mauro Frate (MfA_architects), this structure was engineered by us to stand the test of time and height.
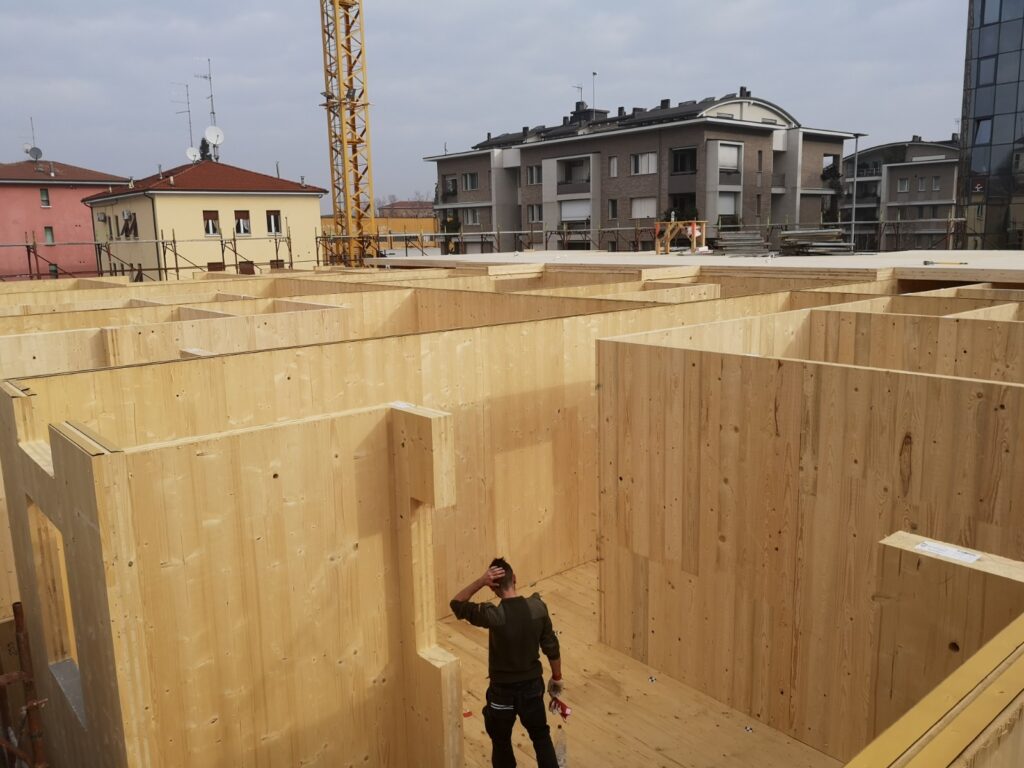
A Heart of Timber
Imagine a building where every inch, from the floors to the walls, even the stairs, is constructed from beautiful timber. This impressive 6-storey structure was built with CLT panels. This choice meets the ever-growing demand for sustainable solutions and embraces eco-conscious practices.
But what sets this building truly apart from others is its heart made of Timber.
Both the stair and the elevator shafts are entirely made of Mass Timber, making timber the sole primary material from the ground up.
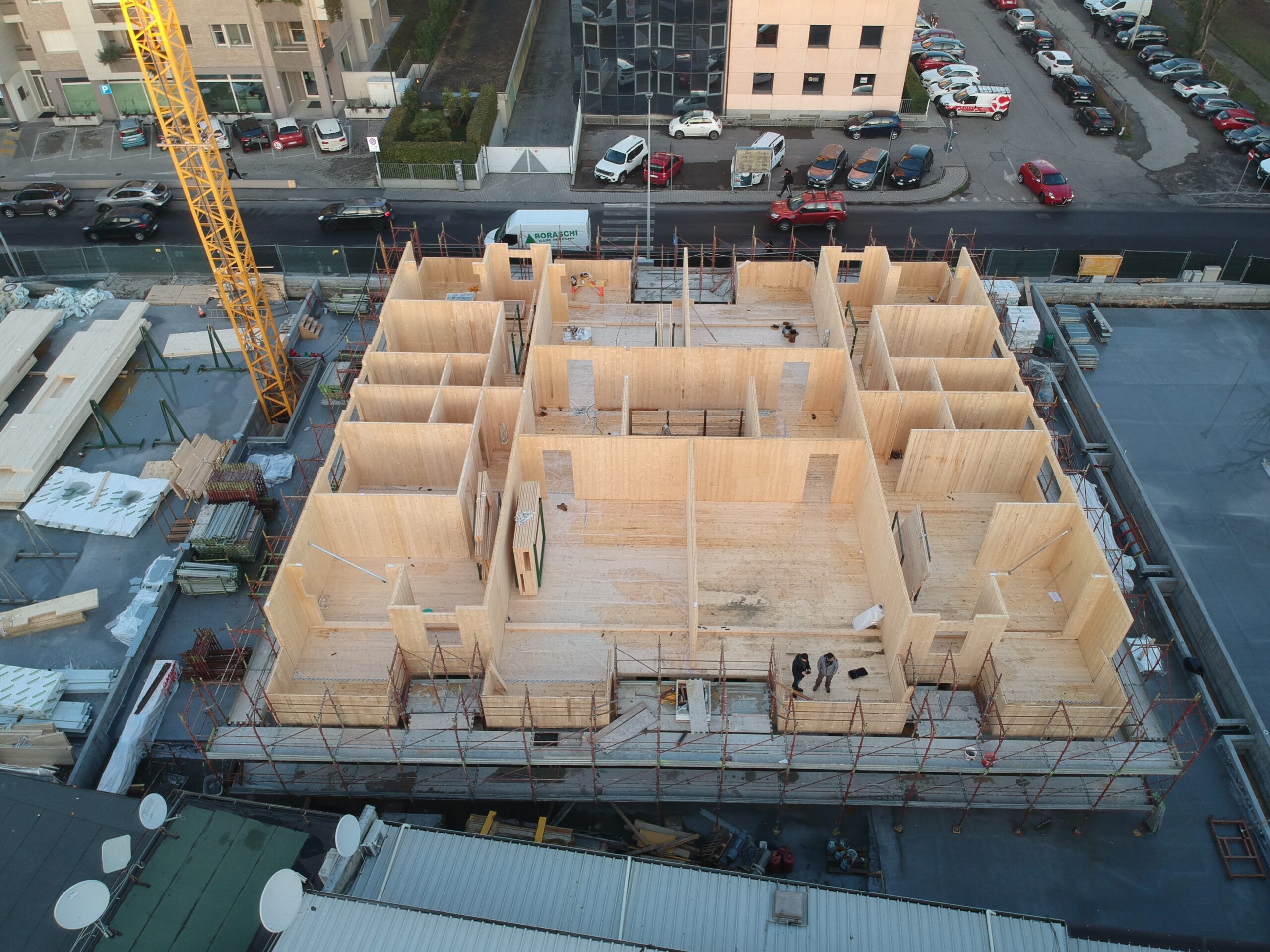
Engineering Marvel: The Stairs
Engineering stairs can be a hard task, but with a touch of ingenuity, even this challenge can be a success. Our approach incorporated Design for Manufacture and Assembly (DfMA), ensuring meticulous care from start to finish. The staircases were pre-assembled off-site and we provided precise assembly instructions to the Boraschi Team. This allowed them to quickly and efficiently install the staircases on-site, saving time and ensuring precision.
Timber staircases can be challenging to engineer, but we have but we did it many times. These experiences have enabled us to develop diverse perspectives and acquire the knowledge necessary to approach this task effectively. In our technical article, we not only discuss timber staircases in detail but also showcase some of our projects that feature them.
WYDIWYG, or “What You Draw Is What You Get,” might sound like a magic spell, and in many ways, it is magical. This principle underscores our commitment to precision and quality. Every detail drawn is faithfully translated to the construction site, ensuring a seamless workflow and the highest quality outcome. This meticulous approach has guided us in designing over 300 projects across 18 countries.
Our Scope of Work
Here, you’ll find the engineering foundation behind this 6-storey structure. Take a journey through the technical efforts driving our designs.
The Devil is in the Details
In the world of engineering, especially with complex timber structures, attention to detail is crucial. For this project, our work was loaded with detailed analyses and solutions. Value engineering allowed us to find the best balance between costs, benefits, durability, and buildability. The Production Drawings, a cornerstone of our DfMA approach, were also filled with details and precise information.
Additionally, a comprehensive structural Finite Element Method (FEM) analysis ensured the building could withstand earthquakes, wind, and fire.
Past and Future meet Today
Timber has been used in construction since ancient times, dating back to 5000 B.C. with the building of stilt houses. However, the field of timber construction has evolved significantly since then. Modern technology has already revolutionized the field when it comes to drawings and analysis, with incredibly powerful software. Is augmented reality the next step? On this CLT building in Parma, we experienced first-hand just how powerful this tool can be. By using AR, construction workers can visualize elements at a 1:1 scale, like an x-ray, to avoid clashes and ensure precise assembly. This revolutionary technology helps minimize errors and helps workers understand exactly where each of the numbered panels must go.
This technology undoubtedly requires knowledge and the right tools, but the benefits that AR offers throughout the lifecycle of a project are tangible and revolutionary.
Gallery