Design Competition for a Multi-Storey Mass Timber Building
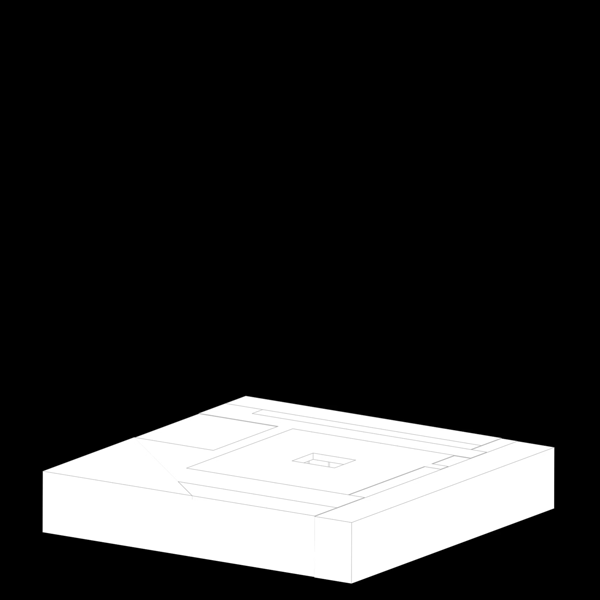
The structural design of a building of this height made of wood is particularly complex and it was not easy to combine the regulatory requirements in force – in terms of calculations – with the requirements of the tender: rapid assembly, “flexible” layout, use of timber for all bearing elements.
To ensure maximum flexibility in the use of internal spaces and to allow changes over time, a complex design choice was made from a structural point of view, i.e. to eliminate all internal load-bearing walls except for those surrounding the stairwell and those forming the edge on the 4 vertices. The floor, as shown in the static diagram below, is therefore supported on the internal walls, on 12 pillars and on 2 lines of beams, as the corner walls are only required to increase the stiffness in the comparisons of lateral loads (earthquake and wind ). This highly innovative system required the development of an ad-hoc connection between the CLT panels capable of at least partially restoring the continuity of moments due to off-plane loads.
With the aim of ensuring the presence of double-height spaces in the first two floors, after careful analysis it was concluded that the best solution from a technical and economic point of view was to use reinforced concrete as a structural material.
All the other floors are made entirely of wood and specifically with Xlam (or CLT) panels for the floors and load-bearing walls and laminated wood for pillars and beams. From the second floor onwards, the concrete is not present as there are no “wet” structural materials; modern dry construction systems have allowed a considerable reduction in the carried weight (<3.0kN / m²) to the full advantage of the dynamic aspects in the event of an earthquake.
Our Scope of Work
Here, you’ll find the engineering foundation behind this 11-storey timber structure. Take a journey through the technical efforts driving our designs.
The analysis carried out went far beyond a simplified feasibility study given the height of the building, and therefore a finite element 3D model was created, which allowed to optimize the sections of the structural elements. The FEM model has been obtained directly from the .ifc file to guarantee the most linear and error-proof data flow possible.
Particular attention was paid to the dynamic behavior in case of horizontal loads and deformability tests were carried out in the event of wind and earthquake. The wind also required a further extremely strict verification regarding horizontal accelerations according to ISO-10137 according to a criterion of comfort. This proved to be the most stringent design parameter. Finally, it is important to underline two fundamental aspects of the project:
- The facades, with the exception of the 4 edges, are made with prefabricated structurally “supported” and not “load-bearing” elements. This allows and facilitates any maintenance interventions over time.
- All the static design was done with the attention of those who daily prepare production drawings for numerous producers of Xlam and lamellar in Europe and beyond. This therefore allows us to guarantee the technical feasibility of the building as of now.